Forged Grinding Steel Balls
Dimensions: 15mm-160mm
Supply ability: 10,000tons per month.
Size≥100mm: Produced by Upsetter Line, Press-Rolling line, Air Hammer Line
Steel Materials: middle carbon alloy steel, its purpose is to reduce its fragility to assure its good toughness and impact in the SAG mill.
Application: Widely used in SAG Mill for gold mines, iron mines and copper mineral processing plants.
The production process is using upset forging and rotary forging. The balls undergo the heat treatment of one quench and twice temper. As a result, the grinding balls of 150mm have a better inner structure and density to improve the grinding efficiency and reduce the grinding balls' consumption.
Size<100mm: Produced by Rotary Rolling Line
Steel Materials: High carbon alloy steel, its purpose is to increase its hardness and further to reduce its consumption to assure its suitable toughness and good wear in the Ball mill and regrinding mill.
Application: Widely used in Ball Mill and regrinding mill for Scraps Grinding, Slag Grinding, Core Grinding, gold mines, iron mines and copper mineral processing plants.
The production process is using rotary forging. The balls undergo the heat treatment of one quench and twice temper. As a result, the grinding balls of 20mm have a better inner structure and density to improve the grinding efficiency and reduce the grinding balls' consumption.
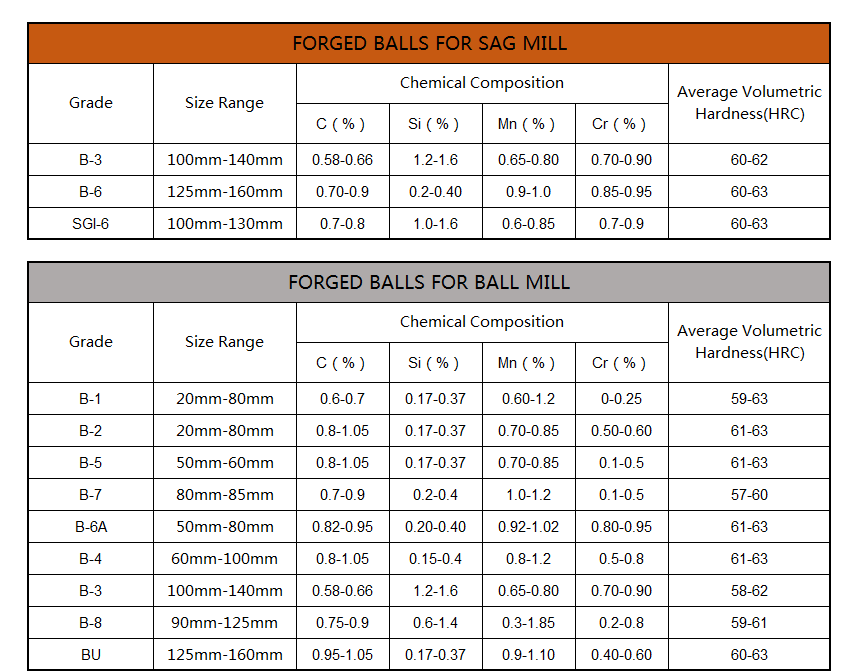
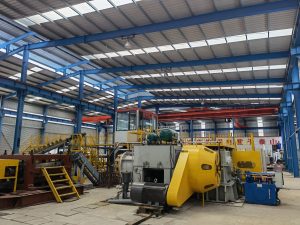
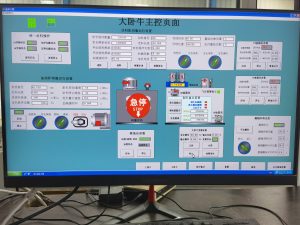
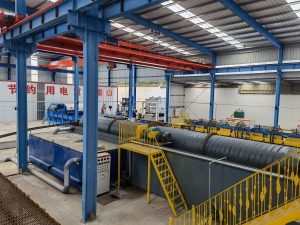

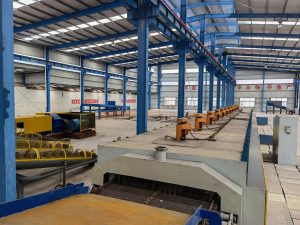
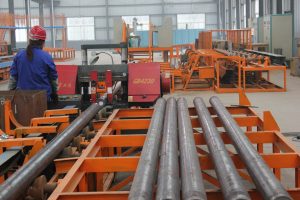
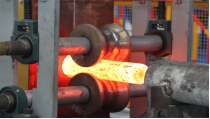
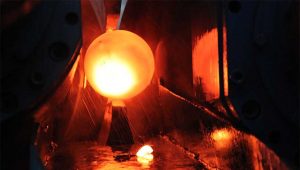
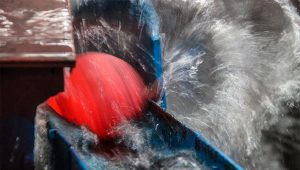
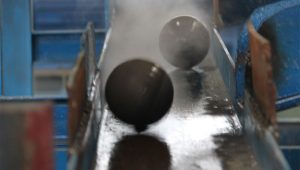
Quality Control
★ Quality Control by Smart Equipment Honwa is always committed to researching and developing new production methods and equipment, to reduce the manual causal influence on the production process and quality. Our equipment can automatically lift bars, heat, forge, separate, and do the heat treatment process. Meanwhile, all figures can be recorded automatically, including how many pieces of bar material, every part of heating data, forging times, ball pieces, heat treatment temperatures in quenching, cooling, tempering. Every process point has its abnormal alarming system, including bar accurate location, ball forging trajectory, gaps between each ball to control the temperatures.
★ Make the First Ball Same as the Last The ball size is of vital importance to the fineness of output to the end-users. Larger grinding media has a smaller grinding surface area but offers a heavier weight that’s generally used to break larger ore. Small grinding media has a larger grinding surface area generally chosen to help make smaller ore smaller. With smart equipment, we can maximize our sizing to make the first ball the same as the last one and optimize ball size according to the operation.
★ Even Wear Our technical team always focuses on even wear ball by balancing hardness and toughness according to the milling targets in the operational plan. Surface hardness may only result in a few hours of good performance while linear hardness will produce consistency throughout the balls’ deployment. The even wear allows for the new life potential of media rejected from ported SAG mills. The rejects are totally recyclable since the media retains their integrity for ongoing deployment in a secondary mill. Recycling to a ball mill as supplementary media or possibly as resale to other users provides additional value for our clients.
★ Focus on Microstructure We check every batch of material by an ultrasonic detector to ensure the hydrogen content of hot rolled bar; We utilize high ratio upset forging to make balls’ microstructure tougher and finer; We monitor heat treatment to lock the right microstructure at the right temperature; We perform ball drop tests of each batch with consistency to ensure performance. We slice balls into pies to analyze its microstructure, grain size, and hardness.

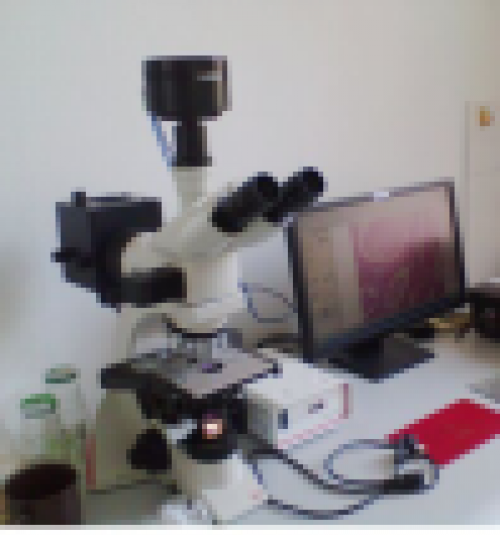

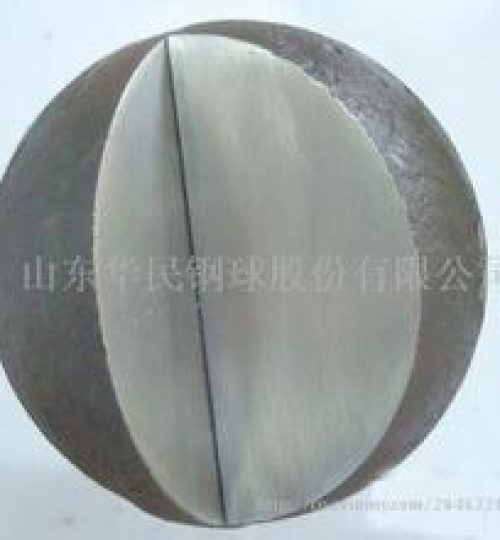
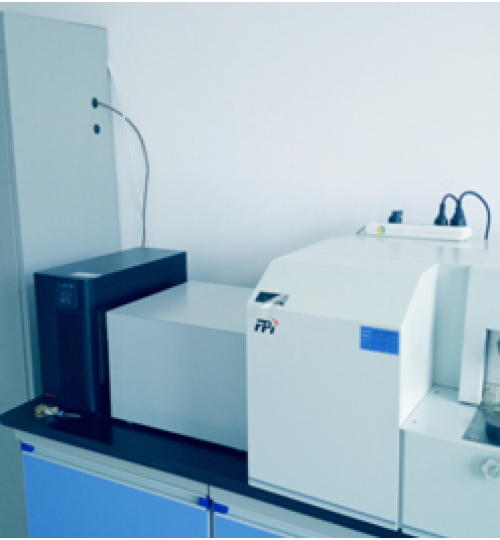
PACKAGING AND SHIPMENT
1).Bags: Ultraviolet-proof Bags,1000kg/bag,1500kg/bag,2000kg/bag. Open at top and bottom, easy to discharge balls.
2).Steel drums: 20mm-40mm:1000-900kg/drum. 50mm-120mm:850kg/drum 130mm-160mm: 800kg/drum
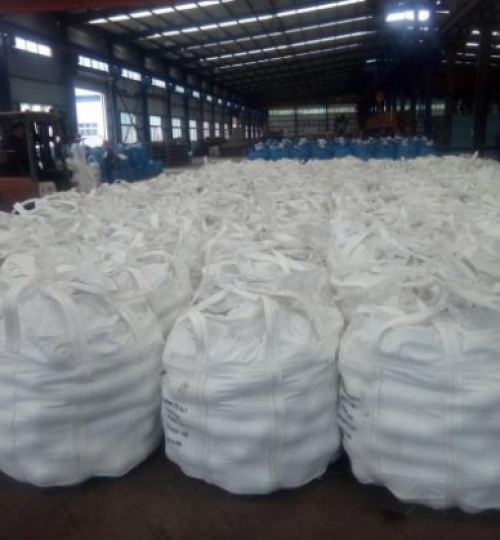
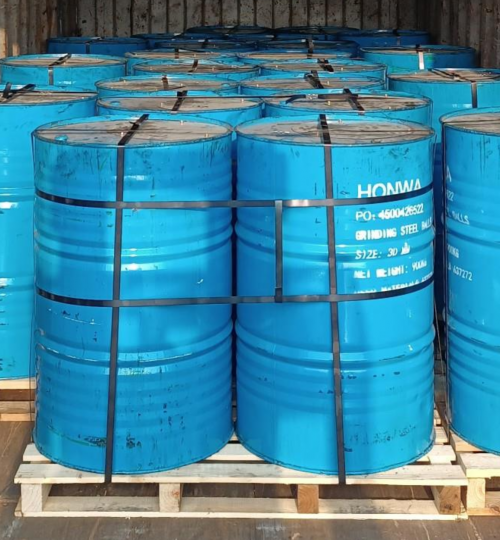


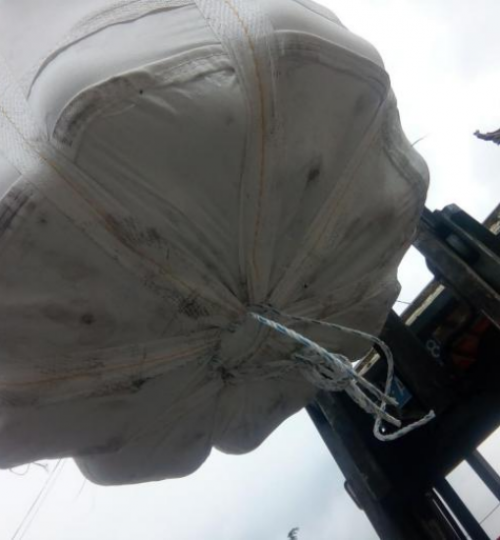